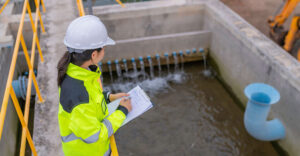
WW200 Wastewater Concrete and Coating
WW200 Wastewater Concrete & Coating is an acid-resistant, low-permeability solution for manholes, pipe linings, and wastewater infrastructure, offering quick curing and lasting protection.
A500 is a sustainable, environmentally friendly, phosphoric acid resistant concrete with all the benefits of ultra high performance Cold Fusion Concrete, and:
A400 Phosphoric Acid Resistant Concrete is designed to withstand exposure to phosphoric acid and other corrosive substances in challenging environments. Its adaptable formulation makes it suitable for various concrete applications in demanding settings.
A500 Phosphoric Acid Resistant Concrete is rigorously tested to meet building code requirements for interaction with conventional reinforcing steel, strength, and modulus properties, ensuring it performs reliably in demanding applications.
All testing is conducted by licensed engineering laboratories, with results verified against our internal quality control standards to ensure consistent, long-term performance. Air-cured test samples are available upon request.
Is A500 Concrete right for your project? Please contact our team for assistance.
Our hands-on approach to training and support sets us apart, providing significantly better service than our competitors. We believe in empowering you with comprehensive training on our products before you apply them, ensuring successful and reliable outcomes.
WW200 Wastewater Concrete & Coating is an acid-resistant, low-permeability solution for manholes, pipe linings, and wastewater infrastructure, offering quick curing and lasting protection.
ST200 Stucco is an acid and mold-resistant solution for commercial and residential facades, offering quick curing, easy application, and superior durability.
SL200 Self-Leveling Concrete is a durable, acid-resistant solution ideal for floor leveling and surface finishing in harsh industrial environments, offering rapid curing and minimal finishing.
Geopolymer Solutions is a leader in cost-effective, sustainable geopolymer concrete and fireproofing materials for industrial applications.
Follow us on LinkedIn for news & industry insights.
© Geopolymer Solutions, LLC | Privacy Policy | Terms of Use